セイコー プレザージュが挑んだ、かつてなき「有田」の壁
琺瑯に漆、そして七宝……。
セイコー プレザージュは、ダイヤルを伝統工芸で設えてグローバルブランドとして日本ならではの美を表現してきた。
その第4弾に選んだのは有田焼。
400年以上の歴史を紡ぐ磁器の技法で作られたダイヤルは、ほのかに青みがかった白で、豊かな透明感すら感じさせる。
日本の匠による新たな美の創造は、かつてないほど困難を極めた。最難関は、薄さと強度との両立。
インダイヤルまで一体成形する多針モデルは、さらに難しい。
日本最古の磁器の産地としてのプライドと情熱とが、今までにない白い磁器製ダイヤルを生み出した。
写真/小澤達也(Studio Mug) 文/髙木教雄 構成/市塚忠義
琺瑯に漆、そして七宝……。
セイコー プレザージュは、ダイヤルを伝統工芸で設えてグローバルブランドとして日本ならではの美を表現してきた。
その第4弾に選んだのは有田焼。
400年以上の歴史を紡ぐ磁器の技法で作られたダイヤルは、ほのかに青みがかった白で、豊かな透明感すら感じさせる。
日本の匠による新たな美の創造は、かつてないほど困難を極めた。最難関は、薄さと強度との両立。
インダイヤルまで一体成形する多針モデルは、さらに難しい。
日本最古の磁器の産地としてのプライドと情熱とが、今までにない白い磁器製ダイヤルを生み出した。
写真/小澤達也(Studio Mug) 文/髙木教雄 構成/市塚忠義
ダイヤルに求められる薄さと強度とを両立させる──有田焼の長い歴史の中でも、これは初の試み。
老舗の窯元と窯業技術センターとが共同で試行錯誤し、新技術を開発することで、有田焼に新境地を拓いた。
日本の磁器の歴史は17世紀初頭、今の佐賀県有田町に始まった。始祖は朝鮮より渡来した陶工の李参平、後の初代金ヶ江三兵衛である。彼が1616年、町を囲む山の一角、泉山で磁器の原料となる陶石を発見し、近くの上白川に窯を築いたことで、日本初の磁器が生まれた。以来、有田は磁器の一大産地として栄え、色絵をはじめとする独自の技術を生み出して行く。その美しさは、早くから海外からの憧憬を集め、ドイツのマイセンやフランスのシャンティイといった名窯が模倣したほど。
磁器の産地として400年以上の歴史を持つ有田町には、今も窯元が数多い。その中で、プレザージュのダイヤル製造を担うのは、1830年創業の老舗「しん窯」。長い歴史の中で培った技術をもってしても、セイコーが求めるダイヤルの品質に至るまでには、4年もの歳月を必要としたという。
「3針モデルでは磁器の厚みは1mm以下、多針モデルでは1.5mmとのオーダーでした。これほど薄い磁器は有田焼400年の歴史でも初。しかも時計に使える強度も必要で、薄く丈夫な磁器をいかに作るのか、その答えがなかなか導き出せませんでした」
と、しん窯の専務取締役にして伝統工芸士の橋口博之氏は振り返る。模索すること1年、朗報が舞い込んだ。佐賀県窯業技術センターが従来の4~5倍の強度をもつ配合陶土を開発したというのだ。以降、同センターと共同で有田焼ダイヤルの開発に取り組んだ。
強化磁器用の陶土は、従来の陶石に含まれる珪石の多くを、ハイテクセラミックで多用されるアルミナに置き換えたもの。このアルミナ強化磁器の焼成後に内部に無数に生じる小孔を最小限にする技術を新たに開発し、ダイヤルとして使えるまでさらに強度を高めた。
続いての課題は、10ミクロン単位で要求される成形精度だ。有田焼の多くは、陶土を水に溶かした泥ショウと呼ばれる液体を石膏の型に鋳込み、成形している。しばらく放置すると石膏が水を吸い取り、陶土が型内で固まる仕組みだ。まずこの型を、従来では用いないCNCマシンを使って切削加工。型自体の加工精度を飛躍的に向上させた。泥ショウの最適な水分量や鋳込み後の放置時間、型から取り出してからの乾燥時間を何パターンもの組み合わせで試し、最適な成形精度が得られる組み合わせを導き出した。こうして高精度に成形しても、焼成時に素地は約20%縮む。均一に収縮するよう、焼成時に素地を置く台は完璧な平滑に磨き上げられている。
「すべての工程が、今までにない新技術でした」と橋口氏。こうして薄さと強度を両立した完璧な加工精度のベースは完成した。しかし、まだ課題は残る。釉薬を、いかに均一に施すかだ。
一番左が型から取り出した後、乾燥させたダイヤル。これをそのまま1300度で焼き、釉薬を施して再び焼くと中央のような艶が生まれる。比べると、縮小しているのが分かる。針穴を加工し、仕上げ焼きすると有田焼ダイヤルのベースが完成する。
泥ショウ作成
陶土と水を混ぜ合わせる。各比率は厳密に計られる。この比率を適性に保つことが安定したダイヤル作りにつながる。
型で成形
泥ショウに圧力を掛けながら、型に鋳込んで成形する。CNCマシンで切削加工した型は、成形精度を維持するために使用回数が限られている。
乾燥
石膏が泥ショウから水分を吸い取り、型内に陶土だけが残る。これを慎重に取り出して自然乾燥。その乾燥時間も規定し、成形精度を高める。
バリ取り
乾燥後は、手に持てるほど硬くしまっている。エッジ部分に残る余計なバリを丁寧にこすり取るひと手間で、真円が得られる。
締焼き(約1300℃)
表面を入念に研磨して、完璧な平滑を保った台に載せ、高温で焼き固める。温度がコントロールしやすい電気窯を使用。焼成で、約20%縮む。
施釉(塗装)
スプレーガンを使い、釉薬を薄く吹き付ける。ダイヤル全体に均一に行き渡るよう、職人は繰り返し技を磨いたという。
セイコー
Seiko
セイコー プレザージュ
有田焼ダイヤルモデル
SARW049
インダイヤルまで一体成形
日付表示とパワーリザーブ計の各インダイヤルは、滑らかな傾斜で窪ませた一体成形。複数の曲面が融合し、表情は一層豊かになった。有田焼伝統の匠の技が、均一な質感と色味をかなえる。自動巻き。径40.6mm。SSケース。クロコダイルストラップ。10気圧防水。20万円。
キャリバー 6R27
現在、時計界で主流の毎秒8振動を刻む自動巻き。ローターはセイコー伝統の両方向巻き上げとし、効率に優れている。パワーリザーブは、約45時間。針合わせ時の秒停止機構を装備。
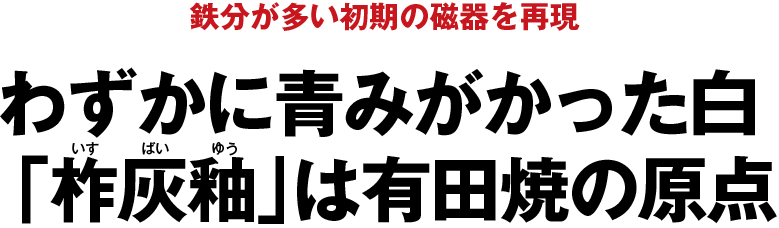
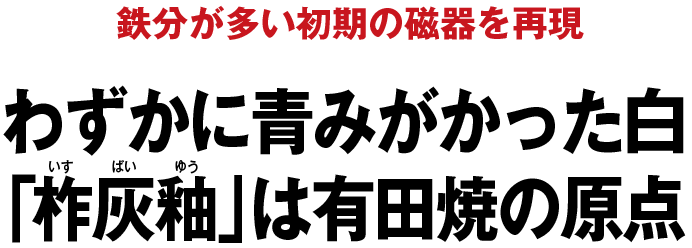
淡い青が浮き、白い透明感が際立つ。初期の有田焼が持つ独特の色味を、プレザージュは再現する。
インデックスは、セイコーの伝統を継承。有田焼400年とセイコー100年の歴史が交錯した。
有田焼は、その初期には前述した町内の泉山で採掘された陶石を用いてきたが、後に熊本県天草諸島の下島で採れる天草陶石が主流となった。埋蔵量が豊富で、今も天草陶石は日本で産出される陶石の8割を占めるという。不純物が少なく、純白に近いのが天草陶石の特徴。つまり有田焼は、素地自体が白い。その表面に釉薬を施すことで、ガラス質の透明な皮膜を形成し、耐水性や強度を高める。
有田では江戸期には、イス(柞)の木の灰を釉薬としていた。わずかに鉄分を含み、それが焼成時に還元されてガラス質に青みがかかる。これを称して、柞灰釉。セイコーとしん窯は、淡い青が透明感を増す柞灰釉の有田焼ダイヤルを目指した。しかし灰を用いた釉薬は、色味が安定しない。そこで現在、有田焼で一般的に使われる釉薬をベースに、それをより艶が出るよう専用調合した。実際の色ではなく、艶でほのかな青を表現するためだ。
ポイントとなるのは、ガラス質に焼き固まった釉薬内に残る気泡の量。釉薬の粘性と融点を下げる調合を模索し、気泡を極力減らすことでほのかな青を表す艶をかなえた。
そして前述した課題である、この釉薬を薄く均一に施すために用いたのが、コンプレッサーによる高圧のスプレーガンだ。これで締焼きしたベースに釉薬を複数回に分けて吹きかけ、薄く均一な施釉を実現したのだ。
釉薬の吹きかけ量は、職人が目視で確認し、品質が均一になるように管理されている。最適な量を定めることにも、かなりの時間を要したという。
施釉後、焼成して釉薬を焼き固めると、柞灰釉の色が表面に浮かび上がる。これにレーザーで針穴やデイト表示窓を加工し、その穴を滑らかにするために再び焼成して、ようやく有田焼ダイヤルは完成する。
仕上げ焼き後のダイヤルを見せてもらうと、わずかにボンベ型になっていることに気付いた。精密成形が要求される中、平坦に形作るよりもはるかに困難なボンベとしたのは、「焼物らしい表現をしたかった」からだという。有田焼の老舗窯元の、プライドである。
そこにインデックスとロゴをプリントするのは、セイコーの役割。それらと針の色に、セイコーは有田焼を象徴する染め付けの呉須色(藍色)に似た、深いブルーを選んだ。セイコー初の腕時計ローレルから受け継ぐ12時インデックスの赤もまた、赤絵とも呼ばれる有田焼の上絵の色と同じで、柞灰釉によく映える。4年を掛け難問を解決した有田焼ダイヤルは、日本の伝統美を誇らしげに湛えている。
新たに生まれた有田焼ダイヤルにプリントされたローマ数字のインデックスは、セイコーの原点である懐中時計「タイムキーパー」を継承する。そして12時だけを赤く染めているのは、国産初の腕時計「ローレル」の伝統を受け継いだもの。
施釉(繰り返し)
釉薬を複数回に分けて吹き付ける。この工程が有田焼特有の色味を再現する上で重要。とても手間のかかる作業だ。
釉焼成(約1000℃)
締焼きと同じ電気窯で、2度目の焼成を行う。1000℃の熱で釉薬は、透明なガラス質に変化し、ダイヤルに艶が生まれる。
寸法検査
専用の検査マシンを導入し、厳しく検査される。多針モデルのダイヤルでは、インダイヤル部分の厚みも計測される。
レーザー加工
許容誤差の範囲内に仕上がったダイヤルは、レーザー加工によって針穴をあける。3針モデルの場合は日付窓を同様に行う。
仕上げ焼き(約1000℃)
レーザーで加工した穴の周囲を均等にならすため、再び電気窯で焼成する。この仕上げ焼きによって、滑らかな縁が得られる。
完成
窯から取り出し、ゆっくりと冷ましてようやく有田焼ダイヤルは完成する。最終的なチェックは、やはり人の目で。橋口氏の眼光が、鋭い。
セイコー
Seiko
セイコー プレザージュ
有田焼ダイヤルモデル
SARX061
柞灰釉が際立つボンベダイヤル
わずかにボンベさせたダイヤルは、受けた光を拡散して柞灰釉の透明感をより豊かにする。日付窓も、レーザーで精密に加工。その周囲も藍色で縁取った。青色とした針の発色も、実に鮮やか。自動巻き。径40.5㎜。SSケース。クロコダイルストラップ。10気圧防水。18万円。
キャリバー6R35
セイコーによる、最新の自動巻きムーブメントの一つ。毎秒6 振動のロービートで高精度をかなえ、約70時間のロングパワーリザーブを実現した。実用性は、極めて高い。秒停止機構装備。
商品の問い合わせ/セイコーウオッチお客様相談室☎120-061-012(9:30~17:30、土日祝日を除く)